- TOP
- SERVICE | AMR
AMR
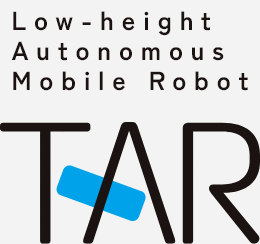
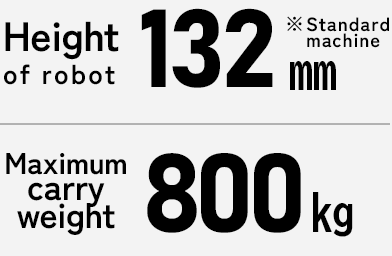
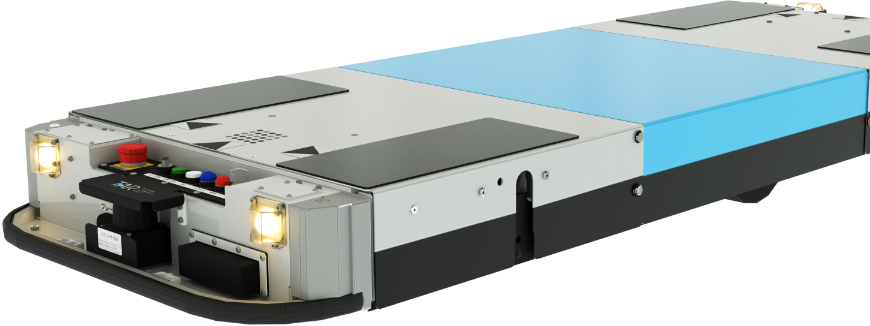
An industry-leading low height of "132mm" and a carry weight capacity of "800kg "make it ideal for transporting basket carts.
TAR is an autonomous mobile robot "AMR" that automatically conveys goods in logistics and manufacturing premises, etc. It cntributes to the automation and labor-saving of factories, and realizes factories where people and robots work together.
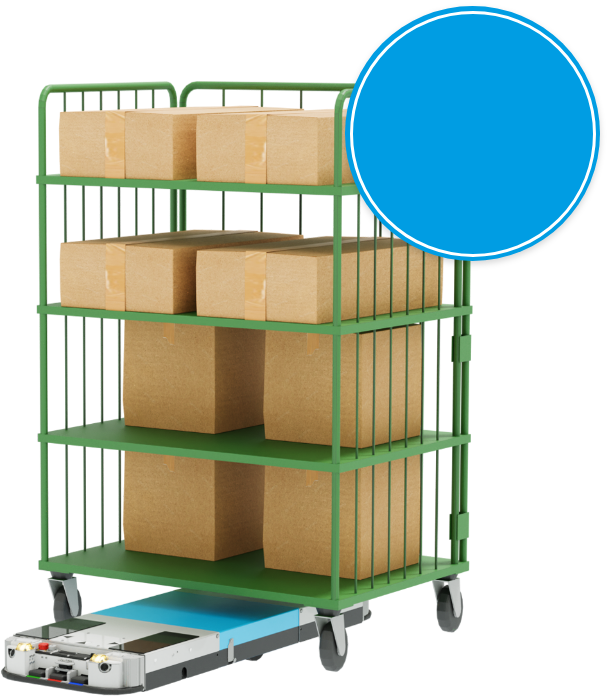
It can be conveyed the basket cart you currently use.
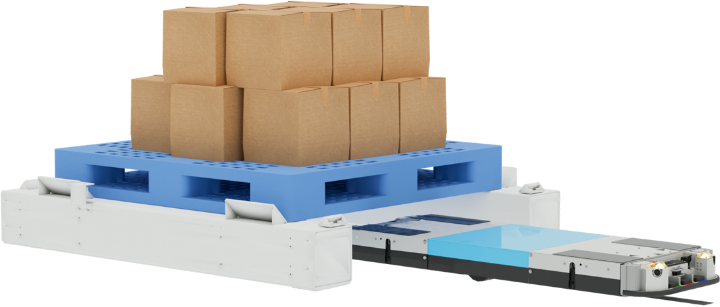
-
Achieving both
low height and
high output -
Pallet transport also
adaptablepallets can be transported as it is by introducing a compatible model with pallet transport.
-
No need to reposition the basket cart even if it is being misaligned.
No need to reposition it even if teh basket cart is misaligned as far as it will be within the set area
-
Automatic charging
functionWhen the battery level is low, it will automatically return to the charging station as "optional" and begin charging.
-
High-precision
positioning
is achievable as wellIn addition to the unique self-location estimation method, achieving highly accurate position control of both stopping and passing place by attaching magnetic tape to areas where precision is required.
(the only applicable for TAR-T02) -
Conveyance is also
feasible for basket
carts placed adjacently
(Row Grasping).Adjacent gripping/non-gripping is possible at specified locations "note there are restrictions depending on the combination of functions"
-
Sufficient safety equipment
To enable collaborative work with humans, the TAR is equipped with a full range of safety characteristic, including the ability to detect and stop people and obstacles, as well as warning functions using turn signals and speakers, and bumper sensors to detect contact.
Front
Emergency stop switch
Lamp with turn signals
LiDAR sensor
Bumper Sensor
Lamp with turn signals
Speaker
Back
Ultrasonic Sensor
Bumper Sensor
Ultrasonic Sensor
Emergency stop switch
-
AMR route
creation toolEasily create AMR driving routes with intuitive operations
Route creation tool featuring user-
friendly UIEasy operation for route and layout changes is also available
-
-
Requirement
definition -
Design
&
Manufacturing -
Installation
-
Maintenance
One-stop solution
We provide one-stop with consistent, in-house customization services from requirements definition until design, manufacturing, installation, and maintenance.
-
-
Pre-implementation support
The system can be verified in advance by executing a proof of concept (PoC) using an actual AMR device when considering its introduction.
Specialized staff will provide comprehensive operation and training during the installation of the equipment.
-
Maintenance services
We provide the following maintenance services to ensure you can use our products for a long time with confidence.
Implementing Preventive maintenance by acquiring
LIFEDATA* Maximize MTBF (Mean Time Between Failures).Regular inspection of an autonomous mobile robot (once a year)
Cleaning, oiling, and replacing work for consumable parts such as running parts
Comprehensive inspection by using safety inspection and dedicated verification software
*LIFEDATA:Accumulated data stored inside the TAR main unit in use
The information desk
Providing information to ensure you use the product with confidence
Recovery support when an error or other incident occurs
System
configuration
example
-
Explanatory notes:
-
LAN cable(STP)
-
Wireless LAN
-
Application
Operation terminal
Route creation tools
-
Middleware
Server
AMR group control system
MES/WCS
Existing
SystemSystem linkage
-
Network
Wireless LAN Access Point
Power supply
hubWireless LAN
Controller -
Robot
AMR
Charger
Automatic
charging
(Optional)
Product specifications and designs are subject to change
without notice in advance for improvement purposes.
Case studies and achievements
Loading and unloading of the logistics warehouse
Without magnetic tapes or QR codes, luggage is automatically delivered at the specified time along the specified route
This is enable to reduce the number of people required for works such as moving delivered goods to designated locations within the warehouse.
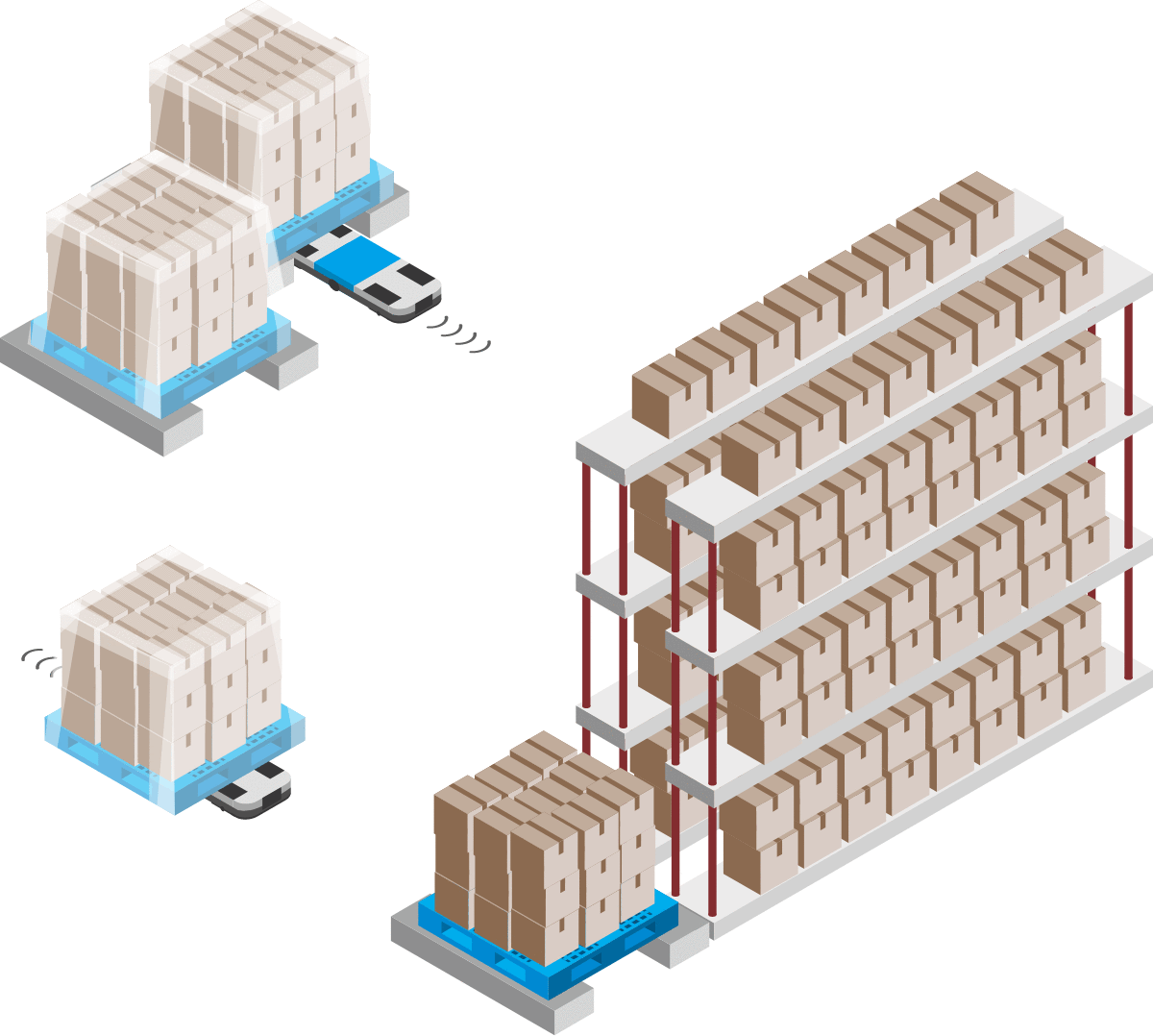
Carry-in entrance
Automatically picks up delivered luggage and transports it to the designated location
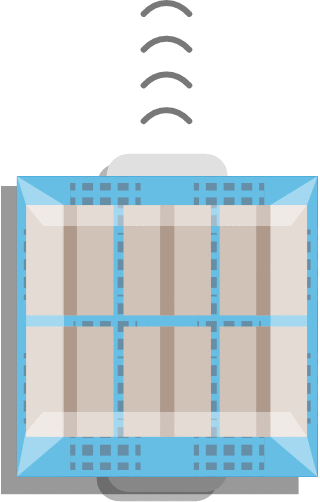

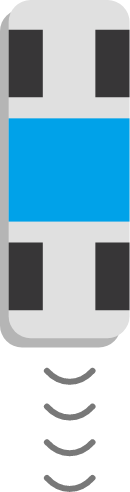
Once the load is unloaded, the robot automatically returns and begins transporting loads again.
Warehouse
Automatic carriage and sorting in logistics warehouses
Basket carts equipped with RFID tag automatically sort items into their designated destinations.
It can be freely changed the destination settings to be delivered and layout.
-
Automatic sorting
to
the locations to
be deliveredUnmanned
transportation utilizes
RFID technology during
delivery. -
Freely change the transport route
Delivery routes and
layouts can be changed
on a PC -
Identification methods other than
RFID also can be accommodatedProposal for identification
method well suited to the
factory and equipment.
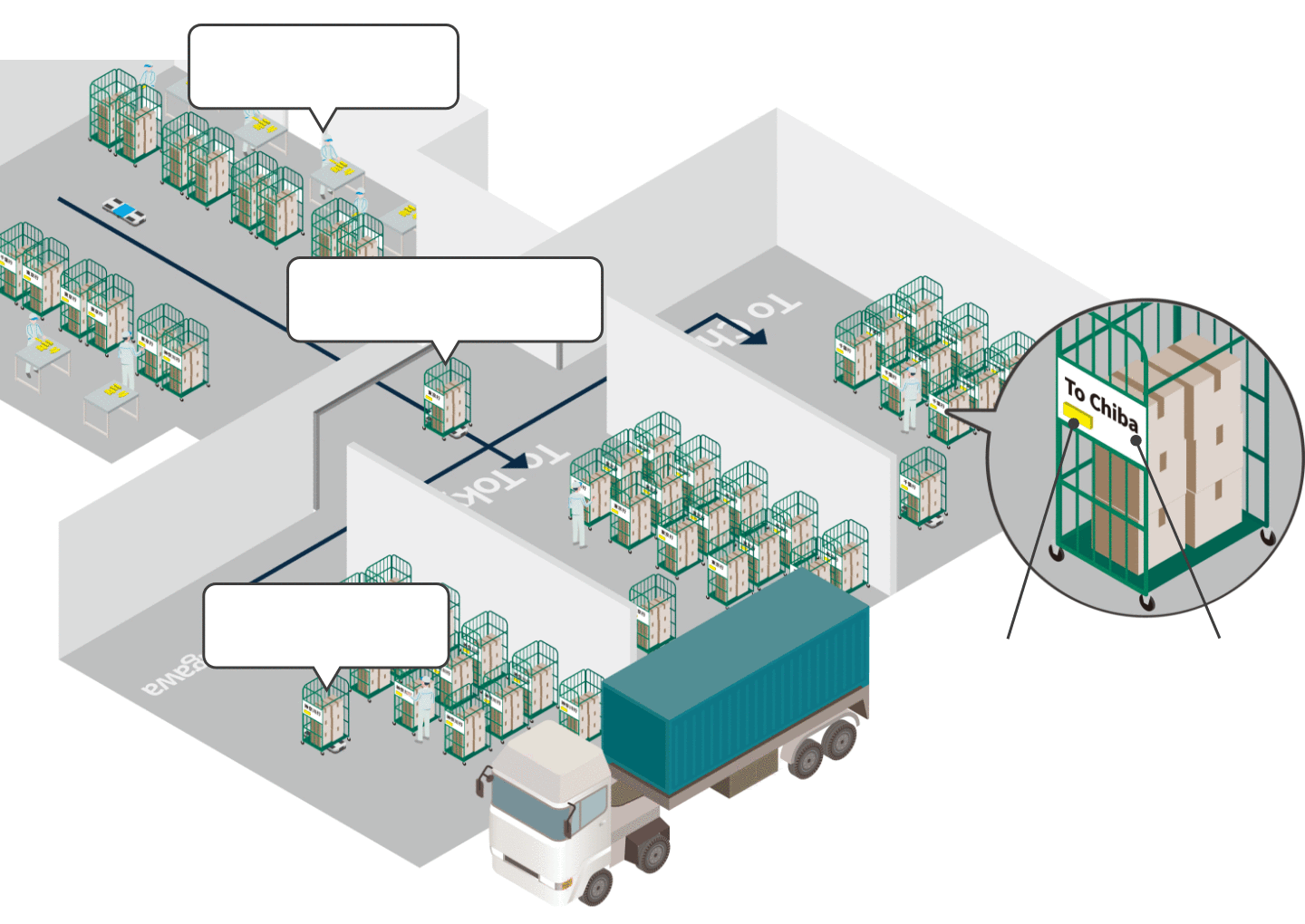
-
A worker attaches an
RFID tag to a basket cart -
The system reads through the
RFID tag on the basket cart -
AMR delivers to each
storage location
-
RFID tags linked to
sorting destinations -
Display for the
sorting destinations
so that everyone
can understand
Manufacturing process transport
Unmanned connection between work processes
The fixed movement of items, such as handing over parts to the next process, can be automated without the introduction of fixed equipment such as conveyor belts, and can flexibly accommodate layout changes.
It is also possible to operate unmanned at set times.
Items can be delivered automatically even at night or during break times when staff are not present, allowing work schedules to proceed efficiently.

work process A
Delivery A's items to the next process at the appointed time
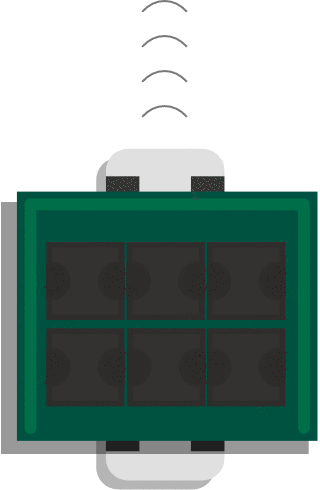

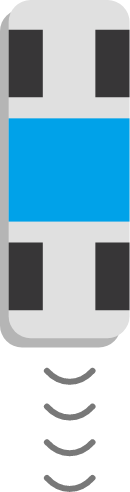
Once the goods are unloaded at process B, the machine automatically returns to process A and delivers the goods again.
work process B
Specification
Equipment Specifications
Product number
TAR-T01
TAR-T02
Main
specifications
Device dimensions
W 1,470 × D 500 × H 132 mm
Device weight
Approx.190kg
Running method
Forward/ backward/turning/carving using two-wheel speed difference method
Movement Speed (max)
Forward: 60 m/min, backward: 12 m/min
Stopping accuracy
TAR-T01±Within 50 mm (unloaded)
TAR-T02±Within 10 mm (unloaded)
Transportable capacity
Maximum 800 kg
Guidance method
Self-position estimation and guidance method based on electronic map
Driving time
Approx. 5 hours (Lithium-ion battery charging time: Approx. 2 hours)
Main functions
Safety function
Emergency stop switch, bumper sensor, step sensor, brake release switch
Obstacle detection
function
Front:
slows down/stops by Laser formula sensor obstacles detection
Rear:
stops by Ultrasonic sensor formula obstacles detection
Caution warning
function
Lamp with turn signal function, speaker
In operation
Temperature: 0 to 40°C, allowable relative humidity 30 to 80%RH (no condensation)
In storage
Temperature: -20 to 60°C, humidity 80%RH or less (no condensation)
External dimensions
Image is for illustrative purposes only
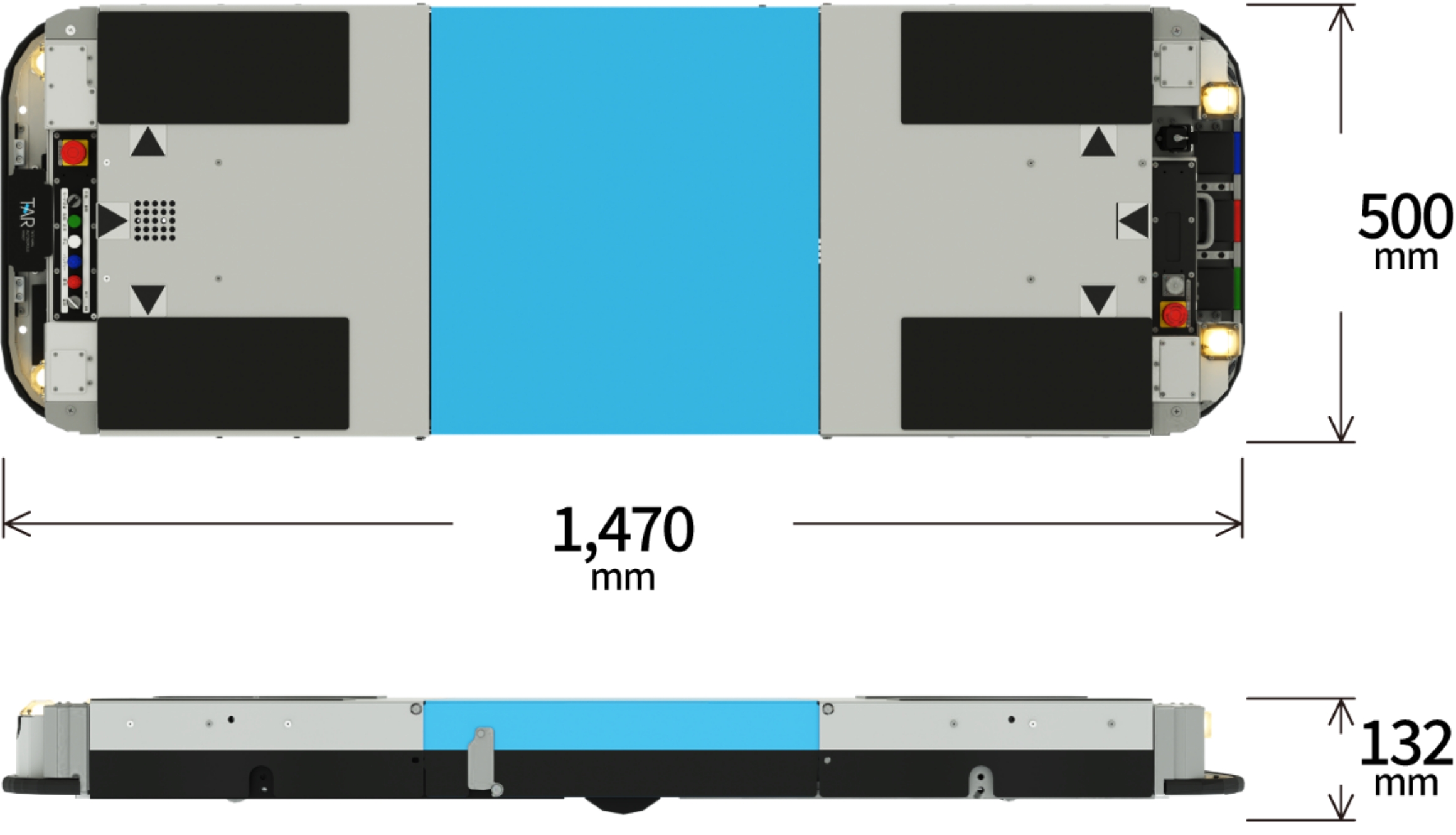
TAR Flyer
Top Frequently Asked Questions
-
Can it be used on a trial basis?
It is possible to actually bring AMR to your environment and check it in advance (fees apply).
-
How many types of size for AMR are there?
Currently, there is only one size of AMR, but the size will vary depending on the various options.
-
Is it possible to operate AMR outdoors ?
This product is intended for indoor use and is not appropriate for outdoor environments.
-
How wide does the aisle need to be?
The specifications state that 1,800 mm is required, but this depends on the conditions. Please contact us for details.
-
How well does it handle bumpy floor surfaces, slopes and trenches ?
The specifications are able to accommodate with steps of 5 mm or less, slopes of 1 degree or less, and trenches widths of 10 mm or less.
-
Is it possible to drive on gratings?
Generally, we do not recommend it. However, depending on the type of grating, it may be possible, so please contact us for more information.
-
Can it be used in a clean room?
It cannot be used in clean rooms.
-
How do I charge to the battery?
You can charge it at any time with the manual charger, or you can have it charge automatically (optional) depending on the remaining power.
-
Is there any way to check the battery deterioration and lifespan?
When it is time to replace the battery, an error code will be displayed on the unit.
-
Can it be used in a freezer storage?
The product is designed for use in environments of 0°C or above and is therefore unsuitable for freezer storage.
-
How do we go about obtaining an electronic map?
An electronic map of the operating area can be obtained by manually driving the AMR unit.
-
Is it possible to operate across floors?
Currently, it is not possible to operate across floors.
cautions
-
In order to operate this autonomous mobile robot, it is necessary to build a 5GHz wireless network, install a dedicated server, and introduce the group control system software.
-
This autonomous mobile robot cannot be used outdoors.
-
There are restrictions on the size of basket cart that can be transported.
-
Please contact our sales department for details.